The Basics of Level Measurement
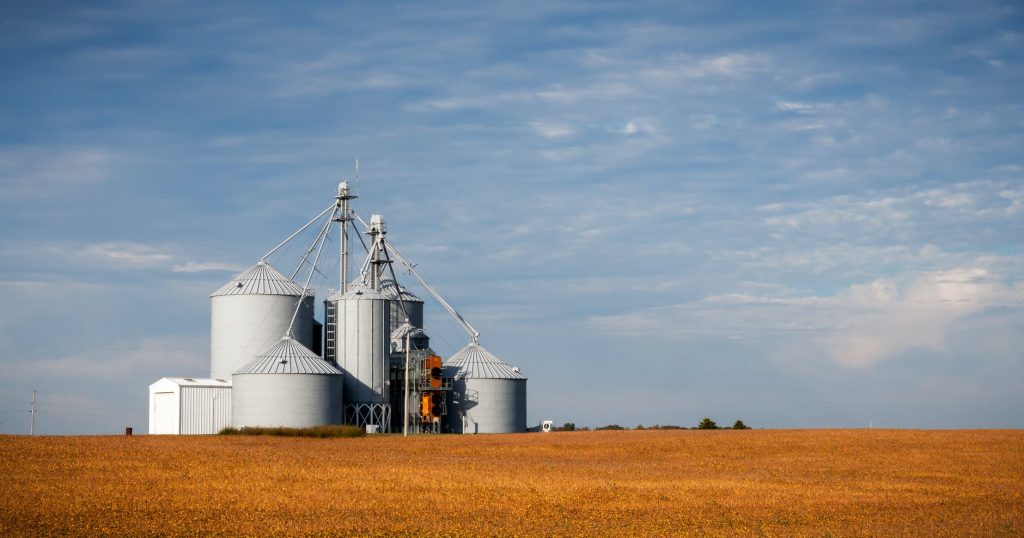
The level of a liquid or solid inside a container can be defined as a distance between the top surface of the material and a reference point.
We have a surprising range of sensor technologies to determine just how much material is in a container. Here is a list of some of the measurement methods and a brief description of these technologies.
- Capacitive
- Differential Pressure
- Floats
- Lasers
- Magnetic
- Radar
- Ultrasonic
- Vibration
Capacitive
Changes in the electrical properties of the space between two electrodes on a switch or between a long probe and the container itself indicate changes in level. These devices include both continuous gauges and point level switches.
Differential Pressure
These measure level based on the pressure difference between the bottom of the container and the head space (for pressurized vessels) or atmospheric pressure for vented containers.
Floats
A mechanical float moves with changing level and a complementary detection technology is used to determine the position of the float displacers. The apparent weight of the displacer varies with level.
Lasers
Laser level devices are top mounted, non contact devices that project a laser beam toward the surface. Time of the flight is used to calculate distance of the material level from the top of the container.
Laser have developed an application niche, especially in the measurement of bulk solids and powders.
Magnetic
These are the variation on the float level devices. A float containing a permanent magnet moves freely up and down.
Radar
These uses a beam reflected radar signal to determine level. Radar is relatively expensive in the more accurate versions.
The radar technology have been increased in recent years. This growth has been driven by high speed processing chips and falling sensor prices as more suppliers make pulse radar components for sensing devices in cars.
Ultrasonic
These operate similarly to radar devices, but calculate level based on the time required for an ultrasonic signal to be reflected from the liquid surface. The sensor emits a high frequency pulse, generally in the 20 kHz to 200 kHz range and then listens for the echo.
Ultrasonic level measurements is the most widely used non contact technology. Ultrasonic level transmitters are used in most industries and are very widely used in open channel flow measurement systems.
Vibration
These detect the presence of liquids or solids based on the shift in resonant frequency of a vibrating probe.
Related Material and Technologies
Name | Description |
KROHNE | KROHNE is a manufacturer and supplier of solutions in industrial process instrumentation. |
VEGA | VEGA is a global manufacturer of sensors for measuring level, point level, pressure as well as devices and software for integrating them into process control systems. |
Massa | Massa manufactures sonar and ultrasonic products for use in the water and air. |
Newark | Newark is a distributor of technology products, services and solutions for electronic system design, maintenance and repair. |
Related Services
If you are interested in our services related to automation or instrumentation and control please feel free to contact MultiSequence at info@multisequence.com or +1 (844) 800-MSEQ
multisequence -
This is good information.